Desktop Metal Qualifies Nickel Alloy IN625 for High-Volume Additive Manufacturing With the Production System
Desktop Metal (NYSE: DM) has qualified nickel alloy IN625 for its Production System platform. This material exhibits high strength, corrosion resistance, and the ability to withstand extreme temperatures, making it ideal for aerospace, marine, and chemical processing applications. The Production System utilizes patent-pending Single Pass Jetting technology for efficient mass production, reducing costs and production time. Key applications include hydraulic spools, turbine blades, and valve plugs. Desktop Metal aims to expand its materials portfolio to enhance manufacturing capabilities.
- Qualification of IN625 enhances product offerings, particularly for high-temperature and corrosion-resistant applications.
- Production System technology significantly reduces production time and costs compared to traditional methods.
- Potential for mass production of complex geometries, boosting efficiency and scalability in various industries.
- None.
Production System Binder Jetting Technology Enables Mass Production of Strong Parts That Withstand High Temperatures and Extreme Environments
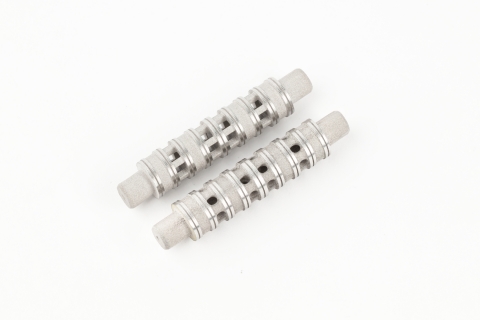
Hydraulic spools are a key oil & gas application that assist in adjusting the flow rates of control valves. IN625 is an essential material for these spools to ensure longevity and withstand highly corrosive environments in oil & gas. (Photo: Business Wire)
A nickel-chromium superalloy, IN625 is characterized by its high strength, resistance to corrosion and oxidation, excellent weldability, and ability to withstand extreme, elevated temperatures for parts under load. IN625 is a critical material used extensively in high temperature aerospace applications, while its corrosion resistance under a range of temperatures and pressures also makes it an excellent choice across marine, power generation, and chemical processing applications.
“As Desktop Metal continues to drive our internal R&D efforts to qualify more materials for the Production System platform, we are excited to offer customers an all-inclusive binder jetting solution to print fully characterized IN625 with excellent properties,” said
“As a transformative combustion equipment company, we are very excited about the release of IN625 for its high temperature and corrosion-resistant properties in flaring and sulfur incineration applications,” said
IN625 - Key Applications
Desktop Metal’s materials science team has qualified and fully characterized IN625 printed on Production System technology in accordance with ASTM testing requirements. IN625 parts printed on the Production System platform not only eliminate the use of tooling and minimize material waste, but also represent a significant decrease in production time and part cost compared to conventional manufacturing methods.
Examples of key use cases include:
-
Hydraulic Spool
Hydraulic spools are a key oil & gas application that assist in adjusting the flow rates of control valves. IN625 is an essential material for these spools to ensure longevity and withstand highly corrosive environments in oil & gas. When produced using traditional manufacturing methods, the spool must typically be assembled from several machined components. With Production System technology, each hydraulic spool can be consolidated and printed as a single part instead of multiple components, significantly reducing the assembly labor costs as thousands can be printed at once with no user input.
-
Turbine Blade
Turbine blades are critical components used in gas or steam turbines in the aerospace industry. These blades are some of the most challenging components to mass produce due to their complex geometries, including organic curves that optimize aerodynamics, and complex cooling channels that ensure the blades maintain an optimal temperature. The Production System enables 3D printing of such geometries, which would otherwise be challenging to produce using traditional manufacturing methods and require advanced casting and machining techniques. IN625 is an ideal material for these blades because of its high tensile, creep, and rupture strength, fatigue and thermal-fatigue strength, and corrosion resistance.
-
Valve Plug
Valve plugs are used for regulating highly-corrosive fluids in chemical processing environments, where corrosion resistance under a range of temperatures makes IN625 an excellent material choice. Traditionally, these parts would be produced using casting followed by a post-machining step for critical dimensions. Since IN625 is a difficult material to machine and the part has complex geometries with organic curves, the conventional manufacturing process would be very expensive with long tooling lead times. In addition, the Production System enables on-demand production of valves in numerous configurations, without the need for a unique, expensive casting tool for each configuration, greatly reducing production costs.
-
Internal Combustion Block
Internal combustion blocks used in aircraft engines often feature extremely complex geometries that are outside the ability of most machine shops and require multiple machining setups and advanced CAM programming. With the Production System, this part can be printed to near net shape without the need for any tooling, and the critical internal dimensions can be touched up in just a few hours with minimal machining setups needed. In addition, because this part experiences extremely high forces and temperatures during the combustion stage, IN625 is an ideal material choice for its incredible material properties in these environments.
-
Four-Way Valve Housing
Valve bodies used in power plants to process corrosive fluids often feature complex internal features, making them difficult or impossible to manufacture as single components using conventional manufacturing processes. IN625 is a critical material for these housings because of its durability and corrosion resistance. Binder jetting this component using Production System SPJ technology enables assembly consolidation, reducing the part count, assembly labor time, and cost to produce the housing.
The Production System - World’s
Created by the inventors of binder jetting and single-pass inkjet technology, the Production System is an industrial manufacturing platform powered by Desktop Metal’s SPJ technology. It is designed to achieve speeds up to 100 times those of legacy powder bed fusion additive manufacturing technologies and enable production quantities of up to millions of parts per year at costs competitive with conventional mass production techniques.
The Production System platform consists of two printer models: the P-1, a solution for process development and serial production applications, and the P-50, a large form factor mass production solution for end-use parts. The Production System combines
In addition to IN625, the materials library for the Production System includes 17-4PH stainless steel, 316L stainless steel, and 4140 low-alloy steel, each of which have been qualified by
To learn more about IN625 and the Production System materials portfolio, visit: www.desktopmetal.com/materials.
About
Forward-looking Statements
This press release contains certain forward-looking statements within the meaning of the federal securities laws. Forward-looking statements generally are identified by the words “believe,” “project,” “expect,” “anticipate,” “estimate,” “intend,” “strategy,” “future,” “opportunity,” “plan,” “may,” “should,” “will,” “would,” “will be,” “will continue,” “will likely result,” and similar expressions. Forward-looking statements are predictions, projections and other statements about future events that are based on current expectations and assumptions and, as a result, are subject to risks, uncertainties. Many factors could cause actual future events to differ materially from the forward-looking statements in this document, including but not limited to, the risks and uncertainties set forth in
View source version on businesswire.com: https://www.businesswire.com/news/home/20211014005708/en/
Media Relations:
carolinelegg@desktopmetal.com
(203) 313-4228
Investor Relations:
jaygentzkow@desktopmetal.com
(781) 730-2110
Source:
FAQ
What is IN625 and why is it significant for Desktop Metal's Production System?
How does Desktop Metal's Production System improve manufacturing processes?
What are the key applications of IN625 in the industry?