Desktop Metal Launches DuraChain™ Photopolymers, an all-new Category of 3D Printable Resins that Delivers Two-Part Material Properties and Durability in a Single Pot System
Desktop Metal has launched DuraChain™, a pioneering line of photopolymers designed for digital light processing (DLP) printing. Utilizing a Photo Polymerization-Induced Phase Separation (PIPS) process, these materials provide exceptional elastic and tough properties. The DuraChain materials, including Elastic ToughRubber™ in various hardnesses, will be exclusively available on the ETEC Xtreme 8K system, enabling resilient, high-performance parts. With a long pot life of approximately one year, DuraChain photopolymers aim to spur innovation in 3D printing, marking a significant advancement in the additive manufacturing sector.
- Launch of DuraChain, a new category of innovative photopolymers for 3D printing.
- DuraChain materials offer enhanced durability and performance compared to standard acrylate resins.
- Exclusive availability on the ETEC Xtreme 8K system enhances market competitiveness.
- Challenges in commercializing the Photo PIPS process due to high viscosity resins and energy requirements.
- DuraChain photopolymers deliver breakthrough elastic and tough material properties for digital light processing (DLP) printing through a Photo Polymerization-Induced Phase Separation (PIPS) process
- Several DuraChain materials – Elastic ToughRubber™ Black and Blanc in various hardnesses – will be exclusively offered on the ETEC Xtreme 8K top-down DLP system
- When illuminated during DLP printing, DuraChain 2-in-1 photopolymers phase separate at the nano level into a material that cures into a resilient, high-performance network
- DuraChain photopolymers will enable a new wave of innovations in 3D printing
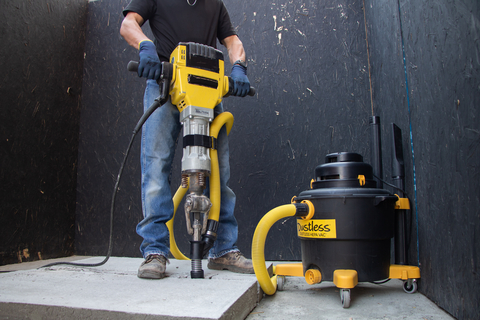
Parts produced with standard acrylate-based resins used in DLP 3D printing today are prone to shattering or fracturing upon impact. For decades, the 3D printing industry has been working to incrementally improve these material properties and deliver more durable and elastomeric properties.
DuraChain photopolymers solve this challenge with a breakthrough approach that leverages the Photo PIPs process to produce tough and resilient end-use parts while eliminating the need for a two-part resin. When illuminated during DLP printing, DuraChain materials phase separate into two parts at the nano level and then cure into a resilient, high-performing network that offers a variety of benefits. DuraChain was developed by
Unlike two-part resins, DuraChain photopolymers demonstrate a long pot life of roughly one year, depending on environmental conditions, making them more suitable for volume production and reducing waste from spoiled, unused material.
“DuraChain photopolymers signal a new era in DLP printing that delivers material properties that compete with thermosets in a long pot-life material,” said
The Challenge of Commercializing Photo PIPS
Photopolymers that cure using the Photo PIPs process have been studied by researchers for years but have not been broadly commercialized – primarily because DLP 3D printing hardware has struggled to print the high viscosity resins required to make use of this process.
Most DLP systems feature a bottom-up printing process in which a projector is placed below the build area and illuminates each part layer through a transparent tray, while the part advances upward suspended to a build tray. Because Photo PIPS resins require more energy to cure and are relatively heavy compared to standard resins, they are challenging to suspend from a build plate during bottom-up DLP printing.
Desktop Metal’s DuraChain materials will be printable on one of the additive manufacturing industry’s only top-down DLP systems, the ETEC Xtreme 8K.
A
Several DuraChain materials will be exclusively available on the ETEC Xtreme 8K: Elastic ToughRubber (ETR) 70 and 90, both of which are offered today and which differ in Shore A durometer value. ETR 70 is available in Black while ETR 90 is available in both Black and Blanc, which produces white parts that can be dyed to any color for production.
ETR is already being used to 3D print end-use parts. A case study showcases how Dustless Tools, a maker of construction and industrial vacuum systems based in
Additionally, a new video also showcases the use of ETR 70 Black by Aerosport Additive, a premium service bureau for 3D printed prototypes and production parts outside of
Parts 3D printed in a variety of DuraChain materials will be on display
About
Forward-looking Statements
This press release contains certain forward-looking statements within the meaning of the federal securities laws. Forward-looking statements generally are identified by the words “believe,” “project,” “expect,” “anticipate,” “estimate,” “intend,” “strategy,” “future,” “opportunity,” “plan,” “may,” “should,” “will,” “would,” “will be,” “will continue,” “will likely result,” and similar expressions. Forward-looking statements are predictions, projections and other statements about future events that are based on current expectations and assumptions and, as a result, are subject to risks and uncertainties. Many factors could cause actual future events to differ materially from the forward-looking statements in this document, including but not limited to, the risks and uncertainties set forth in
View source version on businesswire.com: https://www.businesswire.com/news/home/20220512005585/en/
Media Relations:
lyndamckinney@desktopmetal.com
(978) 224-1282
Investor Relations:
jaygentzkow@desktopmetal.com
(781) 730-2110
Source:
FAQ
What is DuraChain by Desktop Metal (DM)?
Which system is exclusively designed for DuraChain materials?
How do DuraChain photopolymers enhance DLP printing?
What advantages do DuraChain materials have over standard resins?