ZEBRA Consortium Unveils Second Recyclable Wind Turbine Blade, Advances Sustainability in Wind Energy
- Successful completion of full scale validation testing of the first recyclable blade
- Production of the second recyclable thermoplastic blade, measuring 77m in length
- Use of Arkema's thermoplastic liquid resin Elium® known for its recyclability and Owens Corning's high performance glass fabrics
- Incorporation of a new Carbon-Elium® resin spar cap technology and a new adhesive from Arkema's subsidiary Bostik
- World-first use of recycled Elium® resin in the manufacture of a shear web, demonstrating the potential of the resin technology to deliver sustainable blade designs
- Initiation of a further intensive development and testing phase to develop the necessary technologies to manufacture a Carbon-Elium® resin spar design
- None.
Insights
The development of the second recyclable thermoplastic blade by LM Wind Power, utilizing recycled Elium® resin, represents a significant advancement in the wind energy sector's efforts towards sustainability and circularity. The involvement of major industry players like Owens Corning and Arkema indicates a strategic shift towards eco-friendly materials in the manufacturing of wind turbine components, which is a response to the growing global demand for sustainable energy solutions.
From an investment perspective, these developments could signal long-term cost savings and potential market advantages for companies investing in sustainable technology. The successful validation of the first ZEBRA blade and the ongoing testing of the second blade indicate that the technology is not only feasible but also scalable. Investors should note the potential for reduced end-of-life disposal costs and the appeal of such technologies to markets with strict environmental regulations.
However, it is essential to consider the economic viability of these innovations. The complete Life Cycle Analysis expected by June 2024 will provide critical insights into the environmental impact and cost-effectiveness of the ZEBRA blade compared to conventional blades. Investors should keep an eye on these results to better understand the potential return on investment. Moreover, the successful commercialization of this technology will depend on its integration into the existing wind energy infrastructure and the readiness of the market to adopt such innovations.
The second ZEBRA blade's use of a new Carbon-Elium® resin spar cap technology and a new adhesive that is recyclable with the Elium® resin signifies a breakthrough in blade design, emphasizing the wind industry's commitment to innovation and environmental stewardship. The collaborative effort of the ZEBRA consortium, which includes research centers and industrial companies, suggests a concerted industry-wide approach to tackle the challenge of blade recyclability—a known issue in wind energy sustainability.
For stakeholders, the adoption of such technologies could enhance the environmental credentials of wind energy projects, potentially leading to increased support from governments and communities. This could also result in expanded access to green financing and subsidies for projects utilizing these blades. However, the transition to new materials may require significant capital investment and retraining of the workforce, which are aspects that stakeholders must consider when evaluating the long-term implications of such technologies.
While the project's progress is promising, it is important to scrutinize the performance of the blades under real-world conditions and their integration with existing wind turbine designs. As an expert in renewable energy, I would advise investors to monitor the outcomes of the full-scale structural lifetime testing and the forthcoming Life Cycle Analysis to gauge the practicality and economic benefits of this innovation. The potential for this technology to set a new standard in wind turbine manufacturing could have a profound impact on the industry and its supply chain.
The strategic partnerships and technological advancements highlighted in the production of the second recyclable thermoplastic blade could have a substantial impact on the financial performance of the companies involved. The focus on circular economy principles reflects a proactive approach to resource efficiency and environmental responsibility, which could resonate well with environmentally conscious investors and consumers.
Financially, the shift towards recyclable materials may lead to new revenue streams for companies specializing in sustainable materials and recycling processes. It might also open up opportunities for cost reductions related to waste management and regulatory compliance. Investors should be aware of these potential financial benefits while also considering the costs associated with research and development, as well as the implementation of new manufacturing processes.
It is prudent for investors to track the progress of the ZEBRA project and its impact on the participating companies' market positions. As a financial analyst, I would recommend a thorough assessment of the companies' financial health, market trends, and the competitive landscape. This will help determine the potential for long-term value creation through investments in sustainable technologies within the wind energy sector.
- Second recyclable thermoplastic blade built by LM Wind Power in Castellón, with a component made from recycled Elium® resin - a groundbreaking progress in the wind industry's pursuit of circularity
- Owens Corning supplied high performance glass fiber specifically designed to be compatible with Elium® resin- glass fiber represents on average
70% of the blade's weight and is therefore key in the blade's recyclability - This second recyclable blade features a new Carbon-Elium® resin spar cap technology and a new adhesive from Bostik, recyclable together with the Elium® resin
- Full-scale structural lifetime testing of this second ZEBRA blade has started; first ZEBRA blade successfully validated
- A complete Life Cycle Analysis work to compare the environmental impact of ZEBRA blade and conventional thermoset blade is expected end of June 2024
CASTELLÓN, SPAIN / ACCESSWIRE / December 18, 2023 / The ZEBRA (Zero wastE Blade ReseArch) consortium today announces the successful completion of the full scale validation testing of the first recyclable blade and production of the second recyclable thermoplastic blade, further advancing the wind industry's commitment to achieving a circular economy.
The second blade, measuring 77 m in length, was made at LM Wind Power's blade plant in Castellón, Spain, using Arkema's thermoplastic liquid resin Elium® known for its recyclability, and Owens Corning's high performance glass fabrics. It features a new Carbon-Elium® resin spar cap technology and a new adhesive from Arkema's subsidiary Bostik specialized in adhesive solutions.
Importantly, the second ZEBRA blade is a world-first in using recycled Elium® resin in the manufacture of a shear web, which is a structurally important component of the blade, and demonstrates the potential of the resin technology to deliver sustainable blade designs and simulating the circularity of the Elium® resin.
"The ZEBRA project is proceeding according to schedule and will soon deliver its final results. The successful achievement of the test campaign on the first blade and the completion of this second blade represents a major achievement both for the consortium and for the wind energy industry as a whole. The next major milestones for the year 2024 will be the delivery of a complete life cycle analysis based on the blades produced in the frame of ZEBRA project, the focus on recycling activities and the completion of validation testing on the second blade containing the new Carbon-Elium® resin spar cap," emphasises Guillaume SANA, project leader at the IRT Jules Verne.
Following the manufacture of the first recyclable blade in March 2022, the ZEBRA consortium initiated a further intensive development and testing phase to develop the necessary technologies to manufacture a Carbon-Elium® resin spar design. This included material and process development to ensure that required mechanical properties could be achieved, and in close collaboration with LM Wind Power's skilled Castellon team, the necessary manufacturing process could be developed to ensure the manufacture of full-scale components.
John Korsgaard, Senior Director, LM Wind Power says: "The second ZEBRA blade builds on the learnings and valuable insights gained from the creation of the first blade and has helped us understand the structural potential to use Elium® resin in carbon blades. It complements the efforts led by our partners to demonstrate the recycling technologies for Elium® based composites using glass fiber and even carbon fiber. This blade marks a key milestone for the ZEBRA project and highlights the significance of plant collaboration in new technology development, in addition to supporting sustainability objectives for our company and our customers."
According to Owens Corning: "Our involvement in this consortium is part of our strategy to be "sustainable by design", which means taking into account environmental sustainability from the design phase of products so they can be recycled and reused. The testing done around the first blade produced demonstrated the performance and compatibility of Owens Corning's glass fiber product with Elium® resin and long blade manufacturing requirements. This second blade serves as evidence that our products can maintain the performance and recyclability of even larger wind turbine blades."
The first recyclable ZEBRA blade has successfully completed full-scale validation testing at LM Wind Power's Test and Validation Centre in Denmark, with recycling tests currently ongoing. Full-scale structural lifetime testing of the second blade has already started with successful completion of static testing, where the blade is exposed to the extreme loads.
Launched in September 2020, the ZEBRA project is a unique partnership led by French research center IRT Jules Verne and brings together industrial companies including Arkema, CANOE, ENGIE, LM Wind Power, Owens Corning and SUEZ. The project's aim is to demonstrate the technical, economic, and environmental relevance of thermoplastic wind turbine blades on a full scale, with an eco-design approach to facilitate recycling.
About Arkema
Building on its unique set of expertise in materials science, Arkema offers a portfolio of first-class technologies to address ever-growing demand for new and sustainable materials. With the ambition to become in 2024 a pure player in Specialty Materials, the Group is structured into 3 complementary, resilient and highly innovative segments dedicated to Specialty Materials - Adhesive solutions (Bostik), Advanced Materials, and Coating Solutions- accounting for some
About CANOE - www.plateforme-canoe.com
CANOE is a French R&T provider, specialized in polymer formulation, fiber-reinforced composite manufacturing and recycling process development, recycled fiber reprocessing, sensor integration for SHM, materials characterization and non-destructive testing. CANOE provides R&D services to companies over the whole manufacturing chain value of a composite part from design and prototyping up to pre-series and industrialization assistance.
About ENGIE
ENGIE is a global reference in low-carbon energy and services. With its 96,000 employees, its customers, partners and stakeholders, the Group is committed to accelerate the transition towards a carbon-neutral world, through reduced energy consumption and more environmentally friendly solutions. Inspired by its purpose ("raison d'être"), ENGIE reconciles economic performance with a positive impact on people and the planet, building on its key businesses (gas, renewable energy, services) to offer competitive solutions to its customers. Turnover in 2022: 93.9 billion Euros. The Group is listed on the Paris and Brussels stock exchanges (ENGI) and is represented in the main financial indices (CAC 40, Euronext 100, FTSE
About IRT Jules Verne - www.irt-jules-verne.fr
IRT Jules Verne is a mutualized industrial research centre dedicated to manufacturing. Working closely with production equipment manufacturers and integrators, IRT Jules Verne caters to 4 strategic industrial sectors: aeronautics, shipbuilding, the automotive industry, and renewable marine energy. The IRT team works hand in hand with the very best industrial and academic resources in the manufacturing field. Its vocation is to improve the competitiveness of strategic industrial sectors in France by creating disruptive technologies for manufacturing processes. Its mission is to speed up innovation and technology transfer to factories. In its bid to provide comprehensive solutions up to scale-1 demonstrators, IRT Jules Verne installs and utilises a wide range of exclusive state-of-the-art equipment.
L'IRT Jules Verne bénéficie d'une aide de l'État au titre du programme d'Investissements d'avenir portant la référence ANR-10-AIRT-02
About LM Wind Power - www.lmwindpower.com
LM Wind Power ("Company"), a GE Vernova business, is an industry-leading developer and manufacturer of high-quality rotor blades for onshore and offshore wind turbines with blade services solutions and a global manufacturing footprint, headquartered in Denmark. LM Wind Power has produced over 260,000 blades since 1978, corresponding to 142 GW installed capacity. As part of the Company's sustainability journey, LM Wind Power became the first carbon neutral company in the wind industry in 2018 and is committed to building Zero Waste Blades by 2030.
About Owens Corning - www.owenscorning.com
Owens Corning is a global building and construction materials leader committed to building a sustainable future through material innovation. Our three integrated businesses - Composites, Insulation, and Roofing - provide durable, sustainable, energy-efficient solutions that leverage our unique material science, manufacturing, and market knowledge to help our customers win and grow. We are global in scope, human in scale with approximately 19,000 employees in 31 countries dedicated to generating value for our customers and shareholders and making a difference in the communities where we work and live. Founded in 1938 and based in Toledo, Ohio, USA, Owens Corning posted 2022 sales of
About SUEZ
SUEZ is a major player in environmental services. For almost 160 years, SUEZ has supported local communities and industrial companies in the management of essential services such as water, waste, and air quality. As such, SUEZ produces drinking water for 66 million people worldwide, recovers 2 million tons of secondary raw materials per year, and generates 3.1 TWh of renewable energy from waste. In our ongoing management of the ecological transition and climate change challenges, SUEZ relies on the expertise and commitment of its 35,000 employees (particularly in France, Italy, Central Europe, Africa, Asia, and Australia) to offer high value-added and customized environmental solutions to all its customers. SUEZ's expertise allows, for instance, its customers to avoid the emission of 4.2 million tons of CO2, thus improving their carbon footprint and their impact on climate. With a turnover of nearly 7 billion euros and backed by its expertise and capacity to innovate, SUEZ has strong growth prospects. SUEZ relies on a solid consortium of investors made up of Meridiam and GIP - with
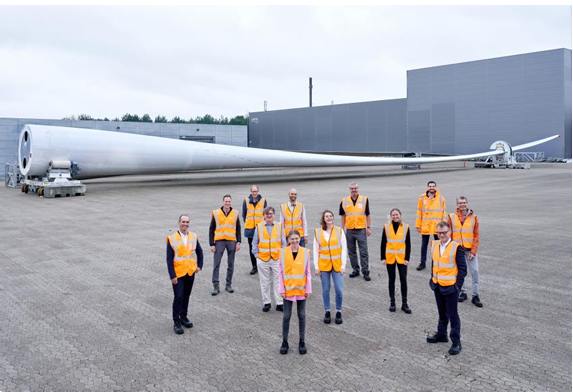
View additional multimedia and more ESG storytelling from Owens Corning on 3blmedia.com.
Contact Info:
Spokesperson: Owens Corning
Website: https://www.3blmedia.com/profiles/owens-corning
Email: info@3blmedia.com
SOURCE: Owens Corning
View the original press release on accesswire.com