World Day for Safety and Health: A Look Into Gildan
Gildan Activewear, a global company with 45,000 employees, prioritizes workplace safety and employee well-being through various initiatives like healthcare support and mental health services. In a recent interview, company executives shared insights on their commitment to safety and health.
- None.
- None.
NORTHAMPTON, MA / ACCESSWIRE / April 26, 2024 / Gildan Activewear:
Q&A with Mike Albright, Vice-President of Health & Safety and Human Resources Manufacturing and Esther Hackett, Vice-President of Human Resources
With approximately 45,000 employees around the world and the majority of them working in facilities, Gildan understands its responsibility in fostering an environment where employees feel safe coming to work. From implementing workplace safety practices guided by its Global Health and Safety Policy, to providing healthcare support beyond work through on-site clinics, health fairs, free medical consultations, and mental health services, the Company is committed to ensuring the holistic well-being of its employees.
In honor of the United Nation's World Day for Safety and Health at Work, we sat down with Mike Albright, Vice-President of Health & Safety and Human Resources Manufacturing, and Esther Hackett, Vice-President of Human Resources, to learn more about the Company's longstanding commitment to Health & Safety (H&S) and how it has become an essential part of the Company's culture.
Can you tell us about Gildan's commitment to Health and Safety?
Mike: Guided by our vision of Making Apparel Better®, Gildan is committed to improving both the quality of apparel it makes and the way in which it produces it; and it's all thanks to our incredible people who manage our manufacturing process from start to finish. Our employees are fundamental to our success, and providing them with safe working conditions, where they may work comfortably and to their full potential, is an important priority for us.
In fact, one of our values is that "we operate responsibly," so embracing a culture of H&S is at the very core of who we are.
Esther: In 2022, as part of Gildan's Next Generation ESG strategy, we further elevated our commitment to H&S by setting a goal to obtain the ISO 45001 certification at all Company-operated facilities by 2028. Since then, we have successfully obtained this certification in all our sewing facilities in the Dominican Republic, and we are on our way to achieving it in our other regions of operation as well.
What role do each of you play in bringing Gildan's H&S goals to life?
Mike: I am responsible for overseeing the implementation of our global H&S management systems and processes across all our manufacturing worldwide; this includes roughly 30 facilities in the United States, Dominican Republic, Honduras, Nicaragua, and Bangladesh. Throughout my time at Gildan, I have been involved in building a strong foundation for H&S, standardizing it across our many facilities, and consistently improving it.
Esther: As the lead of the Human Capital Management ESG committee, I work with various teams across operations to drive our Next Generation ESG strategy target of obtaining the ISO 45001 certification at all our facilities.
Can you tell us more about the ISO 45001 certification? Why did Gildan choose to align itself with this standard?
Mike: The ISO 45001 is an industry-recognized, global management system which promotes H&S among factory employees through a high degree of collaboration between workers and senior management.
Esther: The great thing about the ISO 45001 certification is that it has a laser focus on H&S, so it really pushes us to take a deep dive into our existing health and safety procedures, and make meaningful improvements, tailored to our employees' actual needs. As a Company for which the well-being of its workers is an important priority, ISO 45001 is the ideal standard against which we can enhance our existing systems.
What were some notable changes brought about by the ISO 45001 certification in the facilities in the Dominican Republic?
Esther: At Gildan, we have long encouraged a collaborative approach to H&S management. In all our manufacturing facilities, we have joint management-worker H&S committees which are responsible for reviewing safety performance and identifying opportunities and solutions for improvement.
Yet, one of the most pleasantly surprising developments resulting from the ISO 45001 certification process was an even stronger cultural shift - from factory floor to management - in how H&S was perceived by our people.
As part of this process, plant managers and senior managers engaged in Gemba walks, walking through the factory floor and interacting with employees to learn about the experiences and challenges they face in their day-to-day. This open dialogue facilitated awareness towards the importance of H&S and the ISO 45001 certification, fostering employee engagement and a sense of responsibility among people to maintain a safe work environment, all of which fed into the organization's culture.
Mike: In addition to having our health and safety systems reviewed by external consultants, we trained internal auditors who are now equipped to consistently monitor our processes. The ISO 45001 certification has enhanced our self-sufficiency to make improvements to our H&S measures.
What are some of the challenges you face when standardizing health and safety, across your global supply chain?
Mike: With a supply chain that's global, each of our facilities is at a different stage when it comes to H&S. While some are greenfield projects, others have been acquired, and so our focus has been to create a strong, standardized foundation for H&S.
Esther: Every day we work to continue strengthening this culture of H&S - understanding workers' needs and including them in decision-making processes about H&S-related initiatives. For instance, the knowledge that we gained from successfully obtaining the ISO 45001 certification at our sewing facilities in the Dominican Republic through worker-management collaboration is immensely useful as we move forward with achieving this certification in the facilities of the rest of our regions.
How does Gildan communicate its H&S efforts with a workforce this large?
Mike: H&S's importance is reinforced through every touchpoint on the factory floor, whether it be through formal announcements, updates from leaders, programs, digital communications, and much more.
Recently, we also collaborated with our communications team to identify the main messages we wanted to reinforce globally; these messages are:
- Lead: Leadership leads the way in safety, setting the standard for accountability, commitment, and compliance.
- Empower: Empower and educate yourself and others to create a safe and healthy workplace.
- Act: Every action counts. Act to prevent incidents, report safety concerns, and suggest safety improvements to contribute to a safer work environment.
From there, we built a comprehensive brand and communications platform that would apply to every single H&S touchpoint and rolled out the brand across all H&S initiatives. By doing this, we brought H&S under one roof to have a bigger impact. In addition, this rebrand sent a clear message to all Gildan employees that communicating, empowering, and reinforcing H&S practices across our business is a priority.
In addition to Occupational H&S, what are some other notable H&S measures Gildan takes?
Esther: Our commitment to H&S goes much beyond the workplace. In addition to ensuring occupational H&S, we provide our employees with the support they need to lead fulfilling lives. For instance, our facilities in Honduras, the Dominican Republic, Nicaragua, and Bangladesh are equipped with on-site health clinics. With healthcare being challenging to access in some of these regions, these on-site clinics provide workers with convenient access to medical services and professionals.
At many facilities, Gildan also offers mental health resources such as stress management support in the Dominican Republic, Honduras, and Nicaragua, in-person psychological counselling for employees in the Dominican Republic, and mental health training for our employees in Australia, in addition to our widespread Employee Assistance Programs.
Mike: One of my personal favourites at Gildan is the mega health fairs we host at several of our facilities. As part of these fairs, employees and their families are provided with free medical consultations, lab tests, and other wellness resources to facilitate preventative care.
H&S culture runs deep in our organization, and we are dedicated to continuing to integrate it into the daily lives of our employees.
To find out more about Gildan's respect for people, click here.
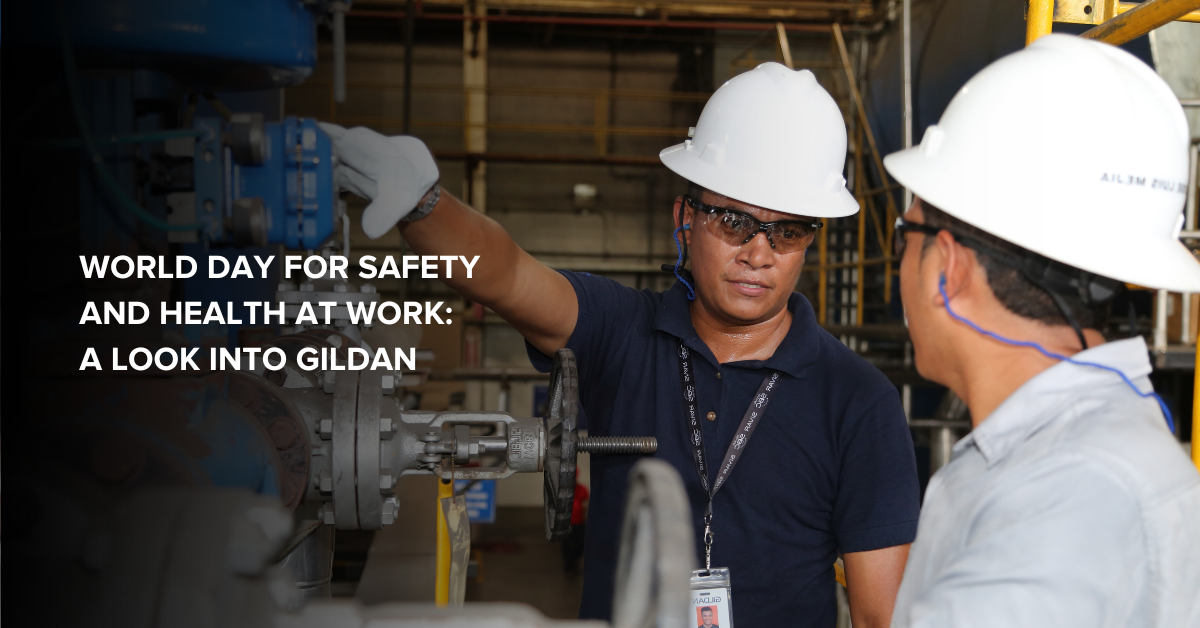
World Day for Safety and Health: A Look into Gildan
View additional multimedia and more ESG storytelling from Gildan Activewear on 3blmedia.com.
Contact Info:
Spokesperson: Gildan Activewear
Website: https://www.3blmedia.com/profiles/gildan-activewear
Email: info@3blmedia.com
SOURCE: Gildan Activewear
View the original press release on accesswire.com