Spirit AeroSystems Hosts Open House at its State-of-the-Art Global Digital Logistics Center
Spirit AeroSystems has inaugurated its state-of-the-art Global Digital Logistics Center (GDLC) in Wichita, a 150,000-square-foot facility aimed at enhancing production efficiency. Funded through a collaboration with the City of Wichita and Sedgwick County, the GDLC features a cutting-edge automated high-bay shuttle system capable of managing over 95,000 unique parts, ensuring 99.97% part kit delivery accuracy. This facility is critical for improving inventory management and production flow, significantly impacting Spirit's operational capabilities.
- Inauguration of the new Global Digital Logistics Center enhances operational efficiency.
- Automated high-bay shuttle system boosts inventory accuracy to 99.97%.
- Facility handles over 120,000 parts daily, improving production flow.
- None.
Insights
Analyzing...
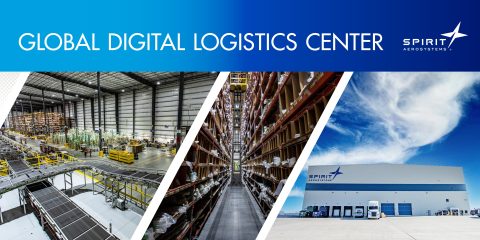
(Graphic: Business Wire)
Funded through a collaboration agreement between Spirit and the
“The Global Digital Logistics Center was created because every part in aviation manufacturing contributes to affordable, high-quality aerospace programs, and this facility has proven to be an essential component in improving our production flow time with precise inventory management,” said Spirit’s Vice President of Supply Chain Execution
Spirit’s leading-edge logistics center is equipped with a 40-foot-tall automated high-bay shuttle system (HBSS) that stores and retrieves more than 95,000 unique parts used in the assembly of large aerostructures, with the capacity to move up to 120,000 parts per day. The center’s shuttle system is the largest and most advanced in the world, driving to
The automated storage and retrieval system includes nine acres of automated rack shelving equipped with robotic cranes that systematically transport totes that travel up to 28 mph and successfully feed 208 kit boxes per hour.
Once parts are received, quantities and other attributes are verified and logged into the system. This triggers the HBSS by dispatching a special tote where employees deposit the unique parts. These designated totes are then propelled into storage where they are continuously tracked.
When a part is needed to assemble a particular section of the aircraft, the HBSS dispatches multiple totes, all containing the required parts to an area referred to as a picking station. At this location, the system directs employees to place the quantity of each part number into each kit box. Once completed with all required parts, kits are loaded onto special carts and seamlessly delivered to the factory floor.
The center’s system is furnished with 83 high-definition cameras that provide real-time visibility to assist with tracking parts, training employees, and assuring the highest level of inventory quality. Additionally, this advanced technology aids in the creation of less waste and provides a safer work environment for employees. To learn more about Spirit’s
On the web: www.spiritaero.com
On Twitter: @SpiritAero
About
View source version on businesswire.com: https://www.businesswire.com/news/home/20210902005512/en/
(316) 523-2479
molly.e.edwards@spiritaero.com
Source: