How Is Plywood Made? A Veneer Mill Tour
- None.
- None.
Take a video tour of a veneer mill to see the step-by-step process involved in making the thin sheets of wood required to make plywood.
ABERDEEN, WA / ACCESSWIRE / February 29, 2024 / Rayonier
Originally published on Rayonier.com
Plywood is crucial in construction, but have you ever wondered how plywood is made? In this article, we explore how trees are transformed during the plywood-making process at a veneer mill in Aberdeen, Washington and the significance of the forest lifecycle in maintaining a sustainable supply of this essential resource, including:
- What is plywood and what is it used for?
- What type of wood is used to make plywood?
- What are the steps to make plywood?
- What happens to the wood scraps in the plywood-making process?
- What happens to the land after trees are harvested for plywood?
- What is the importance of sustainable forestry in plywood production?
What is plywood and what is it used for?
Plywood is an incredibly important forest product used in the construction of all kinds of homes and buildings.
This versatile material is made by bonding together many layers of thin sheets of wood veneer. Consumers choose plywood over other wood building materials such as solid lumber for several reasons:
- Value: A sheet of plywood is more affordable than the same amount of solid wood.
- Strength: Plywood is a very durable wood product thanks to the manufacturing process, which layers wood veneer at varying angles.
- Uniformity: Because of the way they're made, plywood panels can be depended on to come in the width, length and thickness expected without major defects.
What type of wood is used to make plywood?
There is softwood plywood, hardwood plywood and plywood made up of a combination of both. Firs, pines, oaks, maples, birches and other woods are all commonly used to make plywood.
At the Pacific Veneer Mill in Aberdeen, Washington, hemlock, Douglas-fir, spruce and sometimes pine are all types of wood used to make veneer sheets.
Troy Kalinoski, who purchases timber for the mill, says he prefers to buy hemlock wood, which is more affordable and helps the mill keep the overall cost of its product low. In this part of the country, hemlock also has less knots than Douglas fir, making a better quality wood.
"We're probably anywhere from 80 to 85 percent hemlock," he says. "Because of that, our product is coveted by certain customers in our marketplace."
The veneer mill purchases wood from landowners like Rayonier; manufactures it into sheets; and then sells those sheets to a plywood mill. The plywood mill then fastens each thin layer of veneer together into the final product, using a powerful laminate material.
Finding the right wood for the veneer mill
"We try to grow the best logs for the mills that we possibly can," says our Senior Timber Marketing Manager Kevin Pilemalm, who sells Rayonier timber to Pacific Veneer. "Our silviculture team has worked really hard to get good, straight, clean logs that grow fast. There's not really a technique to grow every log on the job to a veneer quality. We have to go out on those jobs and find the veneer quality logs that are there."
Veneer mill logs are more valuable than, for example, lower quality logs Rayonier would sell to a pulp mill. It's the timber marketing manager's job, along with the logging crew, to determine the best use for each log.
"Our guys in the woods are really crucial in picking those logs out and putting those sorts together," Kevin says. "Then, when they come in here, we have the right product and the mill gets what they need."
Kevin says fostering good relationships with customers like Pacific Veneer is key to the role of a timber marketing manager:
"We work really hard to maintain the relationships Rayonier has with our local mills. It's a long-term relationship to keep this industry running."
What are the steps to make plywood? A veneer mill tour.
To make plywood, a tree has to be debarked, steamed in a vault and then peeled into a long, thin sheet at the veneer mill. Those sheets are then graded and cut down to size, dried and stacked. Once the stacks are delivered to the plywood mill, the plywood manufacturing process continues. The veneer sheets are covered in a powerful glue called laminate and then stacked with the wood grain facing in perpendicular directions, which ensures the wood will be extremely strong.
The team at Pacific Veneer provided a tour in the video included with this article, showing the step-by-step process to making plywood sheets. Some manufacturers will make veneer and plywood at the same site. Pacific Veneer specializes only in the veneer manufacturing process.
Below we go into more detail about each of the following steps in how plywood is manufactured, including:
- Step 1: Prepare the logs for peeling in a steam vault
- Step 2: Peel the logs into thin sheets of veneer using a lathe
- Step 3: Clipping and assessing the veneer sheets
- Step 4: Drying, grading and banding
- Step 5: Creating the final product at the plywood mill
Step 1: Prepare the logs for peeling in a steam vault
The first step is to prepare the log for peeling. The mill removes the bark, cuts the logs down to 100.25-inch-long blocks, and places them in steamy vaults.
"Once the vault is full, they go up and turn the water on and shut the door. We're going to cook those blocks at 165 degrees for 16 hours," says Plant Superintendent Dave Newberry.
The steam helps to break down the wood fibers, ensuring a smooth peel and a better-quality end product.
Step 2: Peel the logs into thin sheets of veneer using a lathe
Once the logs are properly steamed, they're ready to peel.
A charger digitally assesses each log, locating the perfect place to hold the log to produce the most veneer. A pendulum then swings back, picks up the log and places it in the lathe, rapidly spinning it.
The machine can peel anywhere from a 7-inch to a 27-inch diameter log. The resulting sheets will be anywhere between 1/200th and 1/10th of an inch thick. The machine can peel up to 14 logs per minute.
The peeler operator listens to the sound of the lathe cutting the log to determine whether it is working properly.
Every two-and-a-half hours, at break time, the lathe blade is replaced with a fresh, sharpened blade. The mill employs a full time grinder operator, whose sole job is to re-sharpen blades for the lathe.
Step 3: Clipping and assessing the veneer sheets
Once the logs have been unraveled into long, thin ribbons of wood, they are moved by a conveyor belt into a rotary clipper.
A digital scanner assesses the wood for defects and directs the clipped to cut the wood into 54- and 27-inch sheets.
Smaller pieces with defects like large holes will drop off the conveyor into a pile that will be used either as plywood filler or it will be processed into wood chips.
A moisture meter scans the 54- and 27-inch sheets to guide how the wood veneer is sorted. There will be heart wood, sap wood, and super sap wood.
Each will be stacked in a separate pile because each will require a different amount of time in the dryer.
Step 4: Drying, grading and banding
The veneer needs to dry in order to prevent decay and improve the properties of the finished wood.
While some plywood mills purchase the veneer at this stage and dry it themselves, others want the veneer sheets in a dried condition.
"It's basically like an oven," Dave says of the industrial dryer. "Once the sheet comes through, it needs to be 8 percent moisture or less."
Once they come out of the dryer, each sheet is graded and sorted depending on the size and quality of the wood.
The mill places a band around each stack of veneer wood and prepares it for the plywood manufacturing customer that will transform it into the final product.
Step 5: Creating the final product at the plywood mill
Once a plywood mill purchases the veneer sheets, they will be transformed into the final product found in lumber and hardware stores.
First, the veneer sheets will be glued. The sheets run through a "glue curtain" that coats them with the laminate, then they're stacked together. The wood grain is rotated between layers, which gives the plywood strength and prevents splitting and shrinkage.
Next, the assembled layers of veneer will be pressed and heated. Using pressure and heat presses the glue into an even, thin layer.
Finally, the plywood panel will go through the finishing process, where it is cut to size, edges are squared and the plywood may be sanded into the final product.
What happens to the wood scraps in the plywood-making process?
Nothing goes to waste in the process of making plywood. For example, bark and wood scraps from the logs are used to fuel the wood-fired furnace that heats the steam vaults and the dryer. The peeler "cores," which are small cylinders of leftover wood once the logs are peeled, are also put to good use:
"Our customers do various things with the peeler cores, from making pallet stock to possibly landscape timbers, and there's various other products they might get used for such as fence posts," Dave says.
What happens to the land after trees are harvested for plywood?
On Rayonier land, harvesting trees for products like veneer is just one step in the forest lifecycle.
Typically within the next one to two years, crews will replant the forest, placing several trees in the ground for every one tree that was harvested.
The next generation of trees will grow for about 40 years - capturing carbon, providing a home for wildlife, and countless other benefits - before it reaches maturity for the veneer and other products the next generation of people will need.
Why is sustainable forestry important in plywood production?
The sustainability of our world's forests is paramount in ensuring we continue to enjoy all the benefits of the forest as well as a continuous supply of fiber for products like plywood.
We use 1000s of forest products in our everyday lives, including lumber but also lesser-known items that rely on tree fiber, such as medicines, phone screens, and bath products including toothpaste, shampoo and moisturizers. You can learn more about products made from trees and why trees are the best raw material for so many items in our ongoing #ItStartsWithTrees story series.
Through responsible forest management practices, we can strike a harmonious balance between meeting the demands of industry and preserving the ecological health of our woodlands.
Want to learn more about the process of making plywood?
Watch this long-form video by Engineering World of how the plywood manufacturing process works in "mega factories."
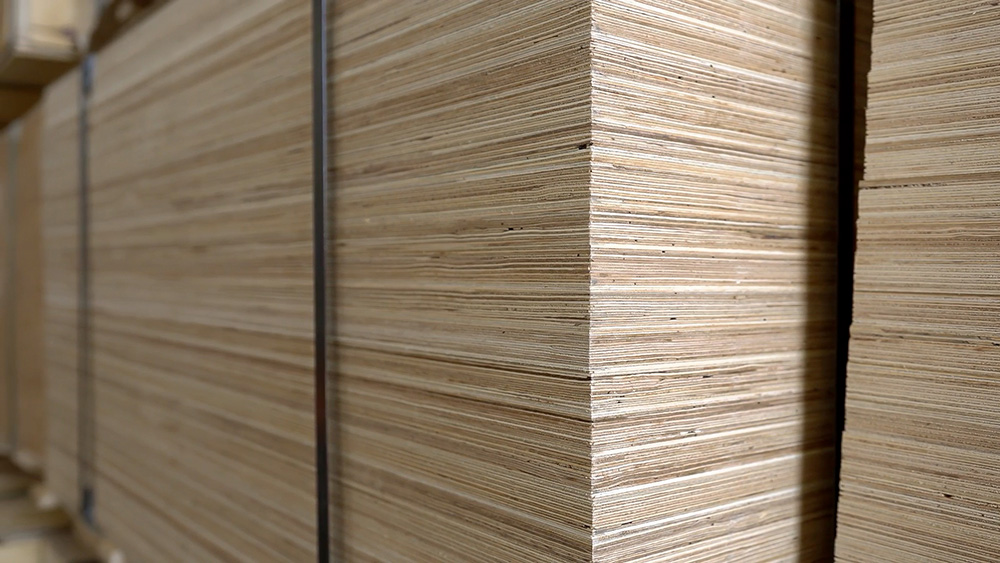
View additional multimedia and more ESG storytelling from Rayonier on 3blmedia.com.
Contact Info:
Spokesperson: Rayonier
Website: https://www.3blmedia.com/profiles/rayonier
Email: info@3blmedia.com
SOURCE: Rayonier
View the original press release on accesswire.com