Molecular Recycling Study Demonstrates a Closed-Loop Solution for Automotive Plastic Waste
A key result: Plastic auto waste met OEM standards for new automobile parts.
NORTHAMPTON, MA / ACCESSWIRE / March 21, 2024 / Eastman
Cars don't last forever, but thanks to a new advanced recycling technology developed by Eastman, some automotive materials can be recycled infinitely.
When vehicles at the end of life are shredded, the leftover materials known as automotive shredder residue (ASR) or "auto fluff" typically ends up in landfills or incinerators. Eastman worked with several partners on a feasibility study that demonstrated successful molecular recycling of ASR.
"Globally, we've reached a tipping point in the automotive industry," said Chris Scarazzo, global automotive segment market manager in Eastman specialty plastics. "Manufacturers have pivoted to more sustainable content, and molecular recycling can definitely play a part in that transition."
That's why Scarazzo is so encouraged by Eastman's collaboration with the United States Automotive Partnership LLC (USAMP); PADNOS, a leading mechanical recycling company; and Yanfeng, a global automotive parts supplier. The 2021 study successfully proved that a closed-loop solution is feasible for automotive plastic waste.
Though a U.S. study, the project is relevant worldwide as regulations are changing. For example, a proposal by the European Commission is pending to repeal the Directive 2000/53/EC on end-of-life vehicles (ELV) and replace it with new requirements. The new directive aims to reduce waste from ELV. Several components in the directive will increase industry sustainability, including a target that at least
Plastics are essential for modern automobiles - but present end-of-life challenges.
ASR is created when an automobile has reached the end of its usable life. The whole car is crushed on a giant conveyor belt and separated into different piles of materials for recycling. The metals, tires and glass that account for
Plastic is essential in modern automobiles because it is light, strong and durable. The industry needs alternative materials to help lower greenhouse gas emissions and reduce carbon footprints. Lightweighting improves fuel economy, and the rise of electric vehicles creates further need for light but strong materials to offset the weight of heavy batteries.
"Modern cars are made with approximately
Molecular recycling - the solution to deliver circularity.
Eastman's molecular recycling technologies can revolutionize recycling because they process hard-to-recycle plastics like those in ASR. These technologies break down plastic waste at the molecular level, so these recycled materials can be built back into new polymers that are indistinguishable from virgin materials with no trade-offs in performance or safety.
Eastman's carbon renewal technology (CRT) can recycle almost any plastic and was used to demonstrate closed-loop recycling for ASR. In the project, PADNOS supplied ASR as feedstock for Eastman's recycling process. Using CRT, Eastman converted the ASR into materials used downstream in the production of new plastic resins. Finally, Yanfeng molded Eastman resins into new automotive parts that met a variety of requirements established by three OEMs: Ford, GM and Stellantis - all members of USAMP.
The results show what's possible.
This study underscored the value of collaboration for a more sustainable future. Both mechanical recycling and molecular recycling are needed and must work together to deliver a recycling infrastructure for the modern age.
"The collaboration on this project is indicative of the work that is needed to create closed-loop and circular-economy solutions," said Kari Bliss, principal of sustainability at PADNOS. "Our purpose statement is on full display with this project - to continue to find ways to innovate, lead and make a positive impact in this world. We are proud to be the mechanical recycler involved in this complex endeavor, which is the first of its kind in North America."
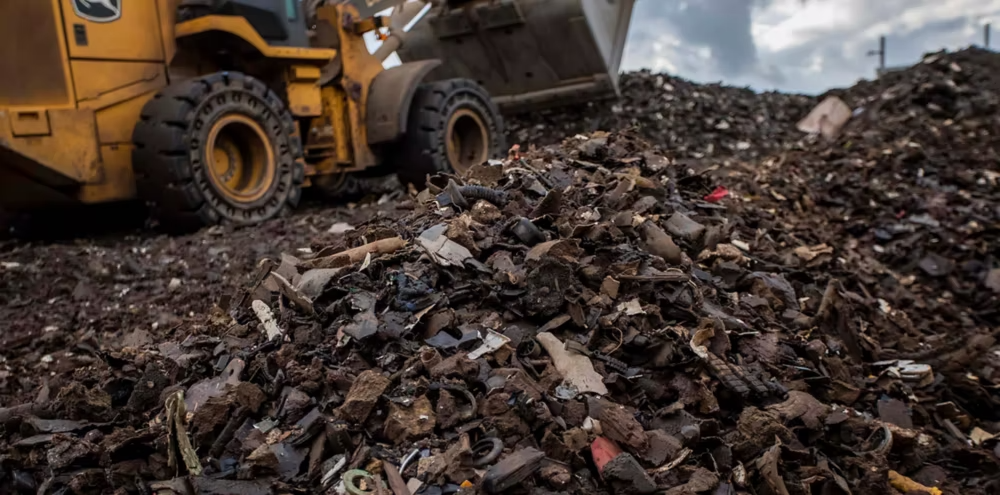
View additional multimedia and more ESG storytelling from Eastman on 3blmedia.com.
Contact Info:
Spokesperson: Eastman
Website: https://www.3blmedia.com/profiles/eastman
Email: info@3blmedia.com
SOURCE: Eastman
View the original press release on accesswire.com